I am at a loss to explain the reasoning behind as to why there are so many spot welds so close together
& in some cases overlapping or on top of one another. My theory being the welder was having a very bad
Monday after not getting laid over the weekend & decided “screw-it” – I’ll vent my frustrations in this way.
This may prove to be a flawed decision on my part to try drill out the spot welds on the parcel shelf
as it was predicated on their close proximity & had the possibility (in my mind at the time) of being the least
destructive method of removing the existing shelf & preserving some of the existing flange/lip for re-attachment
of the new replacement shelf
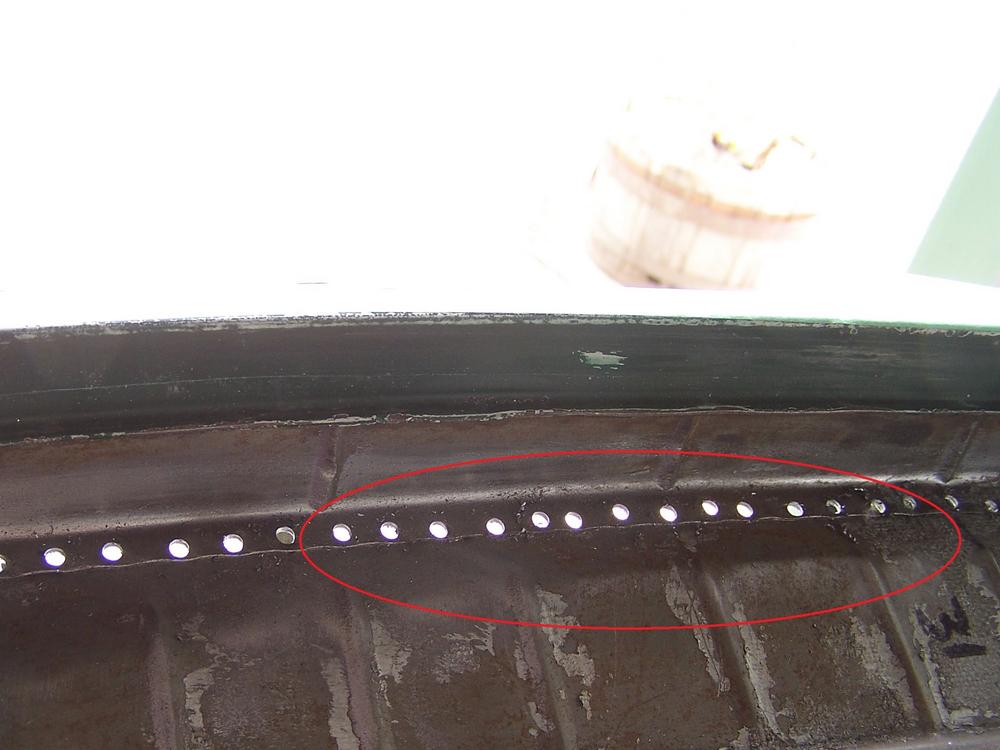
These drilled holes are 3/16” (5mm) & on average 3/8” (10mm) apart. The two surfaces for all intents
& purposes are still conjoined as even a very thin blade hardly slips between the two surfaces. It goes
without saying – this was an abysmal failure.
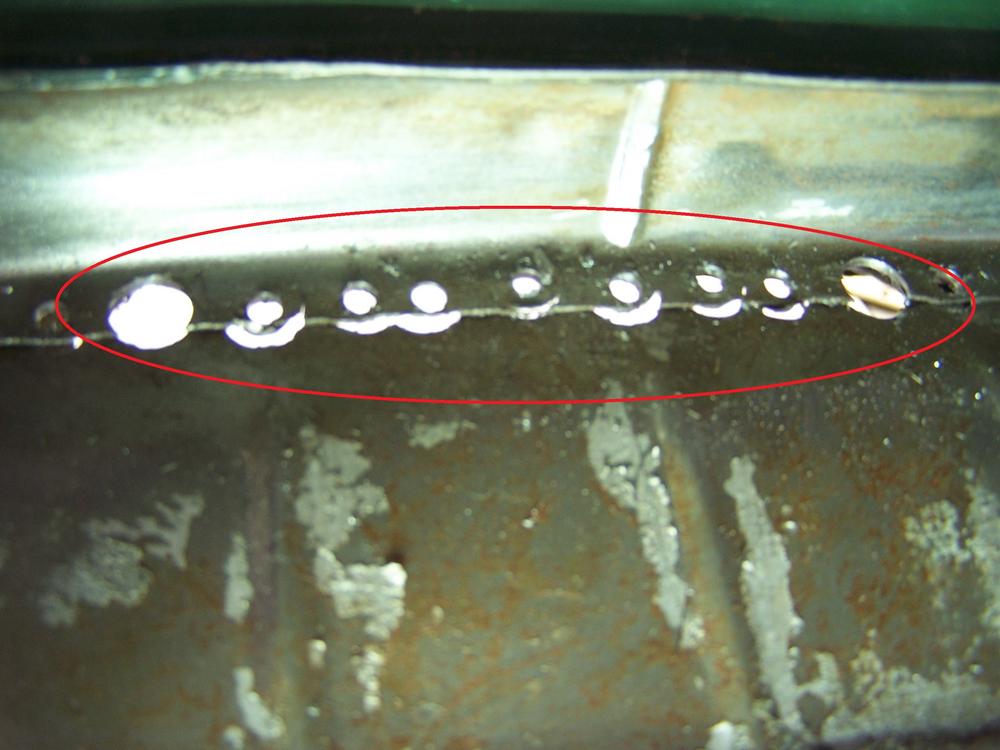
I then used a 3/8” spot weld cutter & still not much in the way of success for as mentioned earlier, the
spot welds being nearly on top of each other as to negate separation of the shelf panel from the flange
in the high-lighted area. There will be precious little of the flange lip left to which the replacement
panel is to be welded if I continue down this course. As you can see, the flange or lip is of such a light gauge
material, it is very easy to blow through it. Again, I cannot get a thin blade between said lip
& the shelf itself.
Can anyone suggest an alternate solution to this quandary or do I continue on with this apparent
destructive process of removal in the hope a Porsche welding guru will be able to make all well
& sound again
Thanks & Cheers
JB